Utility Engineering Company is leading provider of Screw Compressor spares such as Rotary Screw Compressors Oil Air filter OIL SEPARATOR ASSEMBLY MPV VALVE ASSEMBLY AND SERVICE KIT SAFETY VALVE PRESSURE TRANSDUCER And More... in Pune, Maharashtra, India.
Established in the year 2000, We UTILITY ENGINEERING COMPANY, has acquired a recommendable name for itself in the domain of Air Compressor, Spares and Services.
SCREW COMPRESSOR SPARE PARTS
1. Rotary Screw Compressors Oil:-
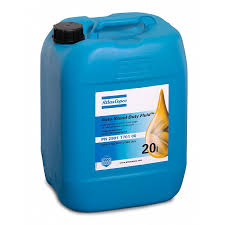
- Exceptional oxidative and thermal stability
- Excellent high & low temperature performance
- Superior wear protection
- Reduced foaming and air entrainment
- Potential energy savings
- Excellent corrosion protection
2. Air filter:-
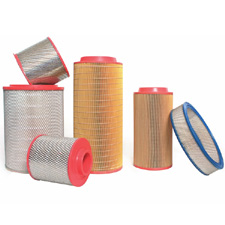
Get clean compressed air by using the right compressed air filters. Protect your pneumatic equipment.
Compressed air filters protect your equipment from dust, dirt, oil and water. Especially when the dirt and dust is combined with oil (which is often the case with compressors), a sticky mess can form inside valves, motors and other compressed air equipment.To protect your equipment, you need to install some compressed air filters. As you can see above, the compressed air filter usually is made up of two main parts: the housing and the filter element.
3. The Oil filter:-
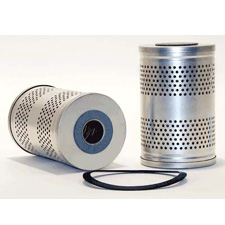
The oil filters removes all the dirt and dust that has collected in the oil.Too much dirt in the oil will damage the screw element. The oil filter has an internal by-pass valve which opens when the pressure difference over the filter becomes too high (when the filter is very dirty or when the oil is still very cold).The oil is now again injected in the screw element to do its job again.
4. OIL SEPARATOR ASSEMBLY :-
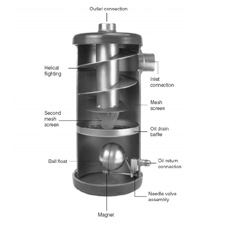
The oil separator is fitted inside the air oil receiver. In the separator, the oil mist is removed prior to the final discharge of the air. Air should only be drawn from the outlet service valves at the end of the oil separator, & should never be taken directly from the air receiver.
After every two years of normal operation as the case may be the oil separator fiber glass discs should be renewed, otherwise, the oil vapors in the discharge air will become excessive.
5. MPV VALVE ASSEMBLY AND SERVICE KIT:-
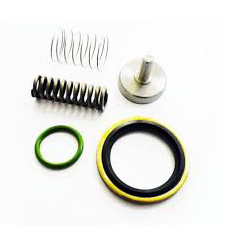
It is of extreme importance that air pressure is developed in the air receiver as soon as the plant is started since it is this air pressure in the receiver which circulates the lubricating oil to the compressor unit through the oil cooler, filters & strainers etc.
A minimum pressure valve is fitted at the air discharge end of the oil separator. The purpose of this valve is to maintain a minimum air pressure of 4 kg/cm2g in the air oil receiver.
It is of extreme importance that air pressure is developed in the air oil receiver as soon as the plant is started since it is this air pressure in the receiver that circulates the lubricating oil to the compressor unit through the oil cooler, filters & strainers etc.
The minimum pressure valve is fitted in compressors with the maximum unloading pressure more than 8 kg./cm2g.
6. INLET VALVE ASSEMBLY AND SERVICE KIT:-
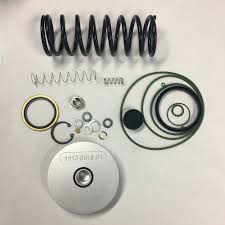
The unloader or inlet valve regulates the capacity of your rotary screw compressor. The air compressor unloader valve regulates the amount of air that is sucked in by your air compressor. By opening and closing the air intake, the capacity of a rotary screw compressor is regulated. This valve is also commonly called an inlet valve or an intake valve.
7. SAFETY VALVE:-
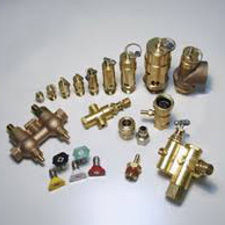
Safety valve is adjusted to 10% higher pressure to maximum unloading pressure. This can be adjusted by tightening pressure transformer fully & by keeping delivery valve open. Start closing the delivery valve till safety valve starts blowing. Note the air-pressure at which safety valve blows. This pressure can be adjusted by adjusting spring tension of safety valve.
Safety valve is adjusted to 10% higher pressure than the maximum unloading pressure. This can be tightening the pressure transformer fully & by keeping the delivery valve open. Start closing the delivery valve till the safety valve starts blowing. Note the air pressure at which safety valve blows.
As the name denotes this is used for the safety of compressor and the manpower working nearby unit. The Safety Valves is adjusted to 10% higher than the Maximum Unloading Pressure.This can adjust by tightening the Pressure Transformer. Tightening the pressure transformer inwards will increase the blow-off pressure setting and vice-versa (keep all Delivery Valves open).
8. OIL CHECK VALVE :-
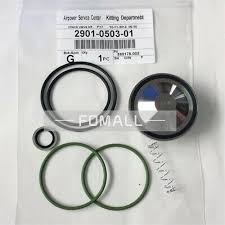
The function of this valve is to stop the supply of oil immediately running through the system after stopping the Air Compressor. Hence Oil is not accumulated in Air End during next starting.
This remains opens when Compressor is running both under load and unload condition.
During Unloading Condition, opens slightly to supply sufficient Oil to Air End. (As there is no air pressure developed during unload condition, there was no heat generation and no extra cooling effect required)
This valve remains open whenever compressor is in running condition both in loading & unloading condition. During unloading condition, this valve opens slightly to supply sufficient oil to air-end. The air-pressure because of scavenging air is sufficient to keep oil-check-valve open.
9. Minimum Pressure Valve (MPV):-
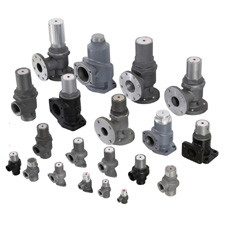
It is of extreme importance that Air Pressure is developed in the Air Receiver instantly as compressor started. Since this Air Pressure Circulates the Lubricating Oil to the Compressor unit through the Oil Cooler, Filters, Strainers etc.
Here MPV plays an important role and holds the required pressure.The function of MPV is to maintain Air Pressure of 4 Kg/cm2 in the Air-Oil Receiver. This pressure must be maintained at load or unload condition.
10. By-Pass Valve:-
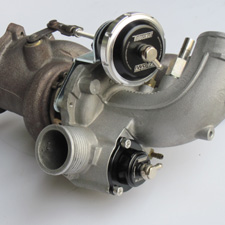
This is fitted with Oil Line between Receiver and Oil Cooler. When Oil Temperature is less than 80-degree centigrade, Oil Cooler is By-Passed. At this condition, Oil flows directly from Receiver to Oil Filter. A Thermostat is fitted in this to sense the temperature of the oil. One Ball Valve is also fitted with Oil Line near By-Pass Valve. If this is closed, Oil will always pass through Oil Cooler. If Thermostat fails to function, the problem can be temporarily solved by closing the Ball Valve.
11. Air Discharge Valve:-
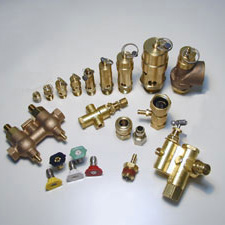
This Valve opens when the Air at Discharge Port of Air End is more than Receiver Pressure. This Remains closed during Unloading Condition when Receiver Pressure is more than Pressure at Discharge Port. Scavenging Air is absorbed through Intake Valves during Unloading Condition to make up for Air Venting out through Unloader Body. A mixture of Oil and Scavenging Air is passed through this during Unloading Condition.
12. Thermostatic valve and kit :-
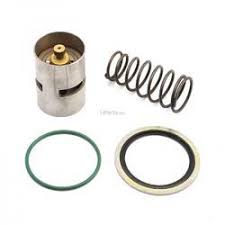
The valve is needed for when the compressor is still cold (after stop) or when it is running in very cold conditions (winter).When the compressor oil is cold, the valve is bypasses the oil cooler so no oil flows through the cooler. This is done to heat up the oil as soon as possible to remove water condensate. Low temperatures are the number 1 enemy of screw compressors.
. The compressor needs to heat up quickly to remove any water condensate as quickly as possible. If you remove it, one of two things will happen: all oil will flow through the oil cooler. Or no oil flows through the oil cooler at all. Probably the second thing will happen as it’s the path of least resistance. If you’re in India and it’s very hot and the compressor is running all the time, than basically this thermostatic valve isn’t doing much.
13. ELECTRICAL PANEL FOAM:-
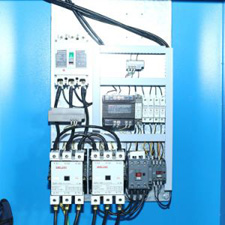
The compressor rack is the most important and complex electromechanical device in the refrigeration system: this delivers cooling for the foodstuffs to all the refrigeration units and related processing rooms.
14. BLOW DOWN VALVE:-
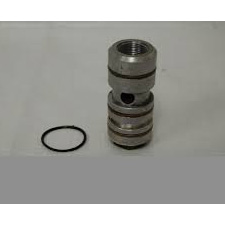
The valve is normally used to vent a pressurized tank. The valve can also be used to recirculate gas from a high pressure to low pressure system. The valve can have an orifice on the exit so that the flow is controlled. The valve is fully pneumatic so that no spring is present. The valve is piloted to act and the system operates to return the valve. The normally closed blow down valve is commonly used to blow down the air/oil separator tank of a rotary screw compressor. The valve is attached to the tank so the tank pressure keeps the valve closed. To “blow down” the tank the valve is piloted open. The piston is designed so that the pilot pressure is less than the tank pressure. The Blow Down valve is a piloted normally open or normally closed valve.
15. PRESSURE TRANSDUCER:-
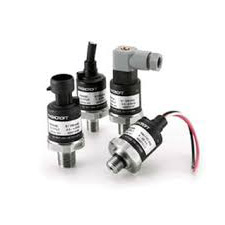
A pressure transducer consists of two main parts, an elastic material which will deform when exposed to a pressurized medium and a electrical device which detects the deformation.
The elastic material can be formed into many different shapes and sizes depending on the sensing principle and range of pressures to be measured. The most common method of utilising the elastic material is to form it into a thin flexible membrane called a diaphragm.